Understanding the Importance of Three Valve Manifolds in Modern Industries
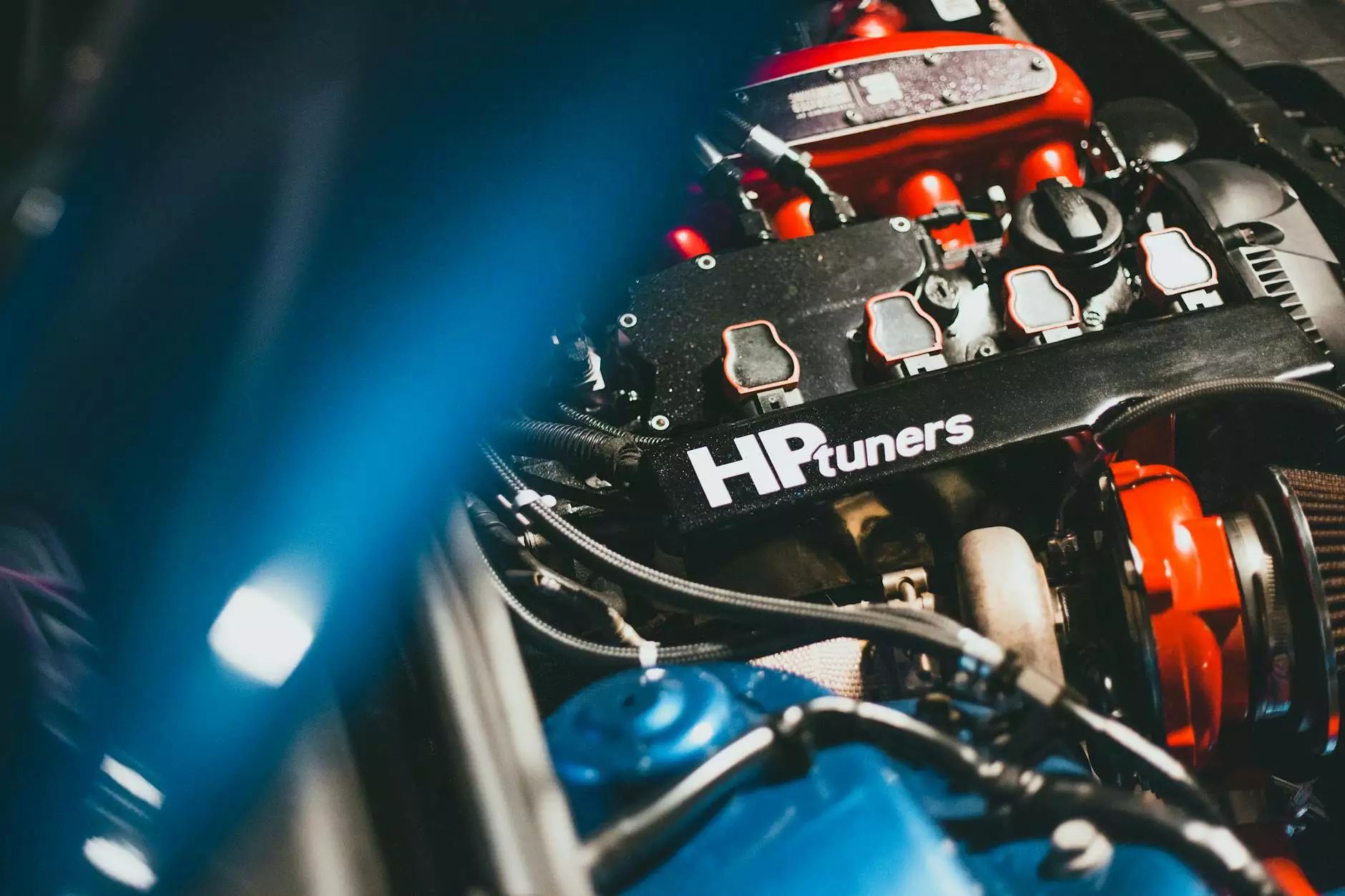
In today’s fast-paced industrial environment, the need for precise and efficient fluid control systems cannot be overstated. One of the key components that aid in achieving this effectiveness is the three valve manifold. It plays a crucial role in various applications ranging from oil and gas to water treatment and manufacturing processes.
What is a Three Valve Manifold?
A three valve manifold typically consists of three valves strategically configured to control the flow of liquids or gases. By regulating the flow, they ensure efficient and accurate measurement, isolation, and venting in various applications. Manifolds simplify piping systems, reduce the number of fittings needed, and minimize the potential for leaks.
Components of a Three Valve Manifold
Understanding the components of a three valve manifold is essential for grasping how it functions effectively:
- Isolation Valve: This valve is used to isolate the process from the measurement system.
- Vent Valve: This valve allows for the venting of the system for maintenance or calibration purposes.
- Measurement Valve: This is the primary valve used to direct the flow to the measurement device.
Applications of Three Valve Manifolds
The versatility of three valve manifolds makes them suitable for various applications, such as:
1. Oil and Gas Industry
In the oil and gas industry, accurate flow measurement is vital. Three valve manifolds are used to connect pressure transmitters to process pipelines, ensuring that readings are taken accurately and isolated when necessary. This is critical for safety and optimizing operational efficiency.
2. Water Treatment Facilities
For water treatment plants, consistent and accurate flow measurement is crucial for maintaining compliance with environmental regulations. Three valve manifolds provide reliable performance, allowing operators to monitor flow rates and pressure easily.
3. Chemical Processing
In chemical processing, the handling of hazardous materials requires precise control. The use of three valve manifolds guarantees that processes can be isolated safely, allowing for maintenance without risking exposure to dangerous chemicals.
Benefits of Three Valve Manifolds
The adoption of three valve manifolds in a variety of industries has several advantages:
- Space Efficiency: They reduce the complexity of piping systems by consolidating multiple valves into a single unit.
- Enhanced Safety: By allowing for the isolation and venting of systems, they help reduce the risk of system failures and accidents.
- Cost-Effectiveness: The use of manifolds can lower material costs and labor expenses during installation and maintenance.
- Improved Accuracy: With a simpler connection to measuring devices, three valve manifolds enhance the precision of readings.
Choosing the Right Three Valve Manifold
When selecting a three valve manifold, there are several factors to consider:
1. Material Compatibility
Ensure that the materials used in the manifold are compatible with the fluids or gases being processed. Common materials include carbon steel, stainless steel, and brass.
2. Pressure and Temperature Ratings
It’s essential to choose a manifold that can withstand the specific pressure and temperature ranges of your application. This will prevent failures and ensure a longer lifespan.
3. Connection Types
Different systems may require various connection types. Ensure the manifold can accommodate the fitting styles used in your application, whether threaded, flanged, or welded.
Maintenance of Three Valve Manifolds
Regular maintenance is essential to ensure the reliability and longevity of three valve manifolds. Here are some important steps:
- Regular Inspections: Regularly check for wear and any signs of leakage, which can indicate issues with the valves or fittings.
- Cleaning: Ensure that the valves and surrounding areas are free from debris and corrosive materials that can impede performance.
- Functional Testing: Conduct routine operational checks to ensure that each valve is functioning correctly. This might include pressure tests and operational simulations.
Cumulative Impact on Industrial Processes
The integration of three valve manifolds in industrial processes significantly enhances system performance. By allowing for safe isolation, precise measurement, and effective venting, companies can significantly improve efficiency and safety standards within their operations.
The Future of Three Valve Manifolds
As industries evolve and technology advances, the design and functionality of three valve manifolds are expected to improve as well. Innovations could include the integration of smart technology, allowing for real-time monitoring and management of flow systems. Such advancements will further enhance the capabilities of these critical devices.
Conclusion
In conclusion, three valve manifolds are indispensable components in modern fluid control systems across various industries. Their design facilitates safer operations, enhances accuracy, and improves cost efficiency. By understanding the significance and application of these manifolds, industries can optimize their processes and contribute to a safer, more efficient operational landscape.
For businesses looking to enhance their fluid control systems, investing in high-quality three valve manifolds from trusted suppliers like TechTubes.in will not only improve performance but also ensure compliance with industry standards.